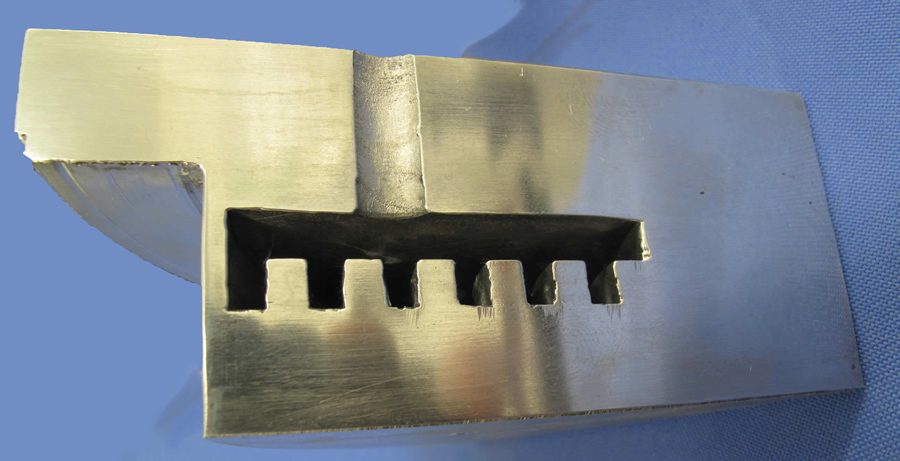
Vacuum Brazing of Aluminium
Introduction
Davis Scientific Treatments has been pioneering the vacuum brazing of aluminium, in many special applications. We use dedicated equipment to overcome the many known difficulties involved in the process.
The need to make joints between aluminium and other materials has been increasing sharply in recent years.
Usage of aluminium has been promoted, in many applications, on account of its low density. Many examples of aluminium jointed assemblies are to be found in aerospace industries.
Many of these applications are in automotive, household and electrical/electronic industries. Mild and stainless steels are often the other material, as is copper, which needs special treatment.
Another increasingly common requirement is to joint ceramics to aluminium especially in electronic applications. The insulation characteristics of a ceramic is often a desirable property [both thermal and electrical]. The lower weight of aluminium is preferred to the use of copper in aerospace applications.
Advantages of vacuum brazing
Brazing has many advantages when compared to other metal-joining processes. Brazing does not melt the base metal of the joint. It allows for better control of tolerances, without the need for extra finishing.
The meniscus, crescent shaped, form of the filler material in the brazed joint is well shaped for reduction of stress concentrations. This factor improves the fatigue resistance properties.
Vacuum brazing is attractive, as it produces higher quality joints than any other known brazing technique. The process is non-polluting, as the brazed surface is free of any contaminants, considered corrosive to aluminium.
Vacuum furnace brazing offers extremely repeatable results. The critical furnace parameters, eg vacuum level and temperature, are uniformly attained with every load.
Capillary joint paths are effectively purged of entrapped gases, during initial evacuation, resulting in more complete wetting of the joint.
Ideal applications for brazing
- Jointing parts of very thin or thick cross-section
- Compact components containing many junctions to be sealed, eg heat exchangers, or deep joints with restricted access
- Joining dissimilar metals, such as copper, and stainless steel, to aluminium, and ceramics to aluminium
- Assemblies with a large number of joints
Difficulties with aluminium brazing
A brazing process is often used to make the aluminium joint. Ideally the technique uses an 'active' filler to produce the joint. The composition of the filler acts directly to 'wet' the two materials, during the brazing cycle.
However, it is well known that, by comparison with steels, the brazing of aluminium is difficult, and there are limitations to the type of components that can be processed.
One of the fundamental criteria that determines the successful outcome, is that the mating surfaces are substantially free from oxide films, as the brazing alloy melts and flows.
Vacuum brazing is a process technique, which is designed to accomplish the removal of the oxide film, before the production of a satisfactory joint is achieved.
In vacuum brazing, it is often necessary to operate at relatively high temperatures, in order to promote the oxide removal process most effectively.
As soon as the heating sequence commences, and when the temperature of the
components is still low, any film which is present begins to increase in
thickness. This happens on account of the chemical reactions with any gases
remaining in the furnace chamber.
Therefore, such a finding is not a surprising result, as often the residual traces in the furnace atmosphere contain some water vapour and oxygen.
Hydrogen gas has been used in this context, being a reducing agent, but is not popular, on account of its incendiary nature.
The key to the successful brazing of aluminium lies in how the removal of oxide films is achieved, throughout the process cycle.
Use of Magnesium
A key component of aluminium vacuum brazing is the use of magnesium, as an additive to the filler alloy, and/or to the base metal of the parts to be brazed.
- When magnesium vaporises at about 570 deg C, it soaks up oxygen and water vapour, thus improving purity of the vacuum
- Magnesium will reduce the aluminium oxide that exists on the surface of the aluminium, to promote uniform accelerated 'wetting' of joint surfaces
- Vacuum brazing using magnesium additives can provide acceptable results for simple applications, eg tube to socket joints
With more complex applications, eg with many joints, or interior jointed assemblies, it is necessary to ensure the joints are shrouded in a 'cloud' of aluminium. Then the filler metal must flow and make the joint.
For these reasons, vacuum brazing with aluminium is very often fraught with difficulties.
It has to be remembered that the presence of the magnesium cloud, in close proximity to the joint, is a fundamental requirement. Pumping must continue during the entire process cycle, as a deep vacuum level, at least 10-4, is an essential parameter. This ensures a very pure oxygen-free environment, with below 0.02 parts per million.
Davis Scientific Treatments (DST)
Here at DST, we have specialised in development of brazing of aluminium, to a number of metals, and to ceramic based materials.
As explained above, the difficulties involved in the brazing of aluminium are considerable. For many years, we have been very active in the conducting of R & D trials to attempt to solve these issues, using a range of commercially important jointing materials.
DST has much R & D experience in this field, gained from many applications.
We have vacuum furnace equipment, which is dedicated to testing any customised
aluminium brazing application, so as to find an effective process solution.