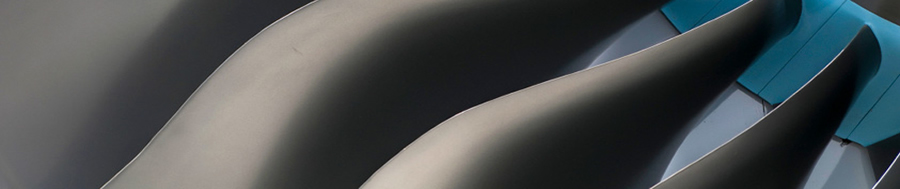
Leak Testing Operations
Leak Testing - General
There are many methods to leak test objects, from simple liquid immersion, to see bubbles and hence find locations of leaks, to the highly accurate use of helium for critical component evaluation.
Pressure and leak test operations are important in the quality of components, assemblies, containment vessels, and other systems. It is a non-destructive method to prove the integrity of equipment.
Davis Scientific Treatments can carry out hydraulic and pneumatic static and dynamic pressure testing. We also offer helium leak test facility. Sometimes the testing must be performed at higher or lower temperatures than ambient, as high as 250 deg C.
Leak Testing Benefits
- It is a clean and effective test
- Results allow calibration to product standards
- Pass or fail conditions can be automated
- Components/assemblies may be marked accordingly
- Results are quantifiable and recordable
Leak Technique Determination
Some of the questions which should be addressed, in determining which technique should be adopted, are as follows:
- Are the parts clean and dry
- Must he parts be kept clean and dry
- Are they flexible or rigid components
- What is the leak test requirement
- At What temperature has the test to be carried out
- Is it easy to seal the assembly for testing
- Is the surface finish critical
- How large is the component
- Are there concealed spaces within an assembly
Hydraulic Pressure Testing
Water, or another specified liquid such as oil, is used for the application of pressure. During testing, the component, or assembly, having been sealed, is subjected to the required hydraulic pressure, for the desired period of time, information coming from the customer.
Determination of acceptance is gained from holding of the pressure, without any pressure losses, leakage, or deformation of the subject parts.
Pneumatic Pressure Testing
With pneumatic tests, air is used to pressurise the assembly or component. This operation is often used in proving sealed systems, or pipework, or other jointed components.
Sometimes dry nitrogen is used as the gas, in place of air, which being inert, acts to keep the components very clean.
Using a pressure gauge to monitor any losses or leakage, the test determines whether a component or assembly will fail in service, and can then be used to provide a pressure rating.
We also can supply your components, sealed with air [or nitrogen] at the tested pressure, for maintaining internal cleanliness.
Proof Pressure Testing
The proof pressure testing technique is used to apply forces to the product, which result in excess stresses, originating from the stated operation pressure.
This is usually performed as a hydrostatic test, using water as the liquid. Such a test establishes a higher proven pressure at which the equipment may safely perform, without any permanent deformation or damage.
Certification is usually provided to record the details of the test.
Our staff can help you to find the safe operating conditions for your products and equipment.
Helium Leak Testing - General
Helium is used for leak testing critical and safety-important products. These include many aerospace components, motor safety bags, pipeline welding, pacemakers, in a wide range of industrial processes.
Helium is a commonly used gas, as it has many advantages:
- it is an inert gas
- it has low concentration in air
- it is non-toxic
- it is an odourless gas
- has very small atomic size, ideal for small leaks detection, down to 1/1000,000,000 mbar, l/sec.
Helium Leak Test Process
The test component, or assembly, is placed inside the testing chamber, which is connected to a vacuum pump. The pump evacuates the air from both the test piece and surrounding chamber, to the initial vacuum required.
Then the piping is configured to only permit further vacuum to be drawn on the test chamber only. The test chamber will be at lower vacuum than the test assembly.
At this point, helium gas is introduced into the chamber. A mass spectrometeris used to measure the sample vacuum of the chamber, as it's vacuum level falls further.
The mass spectrometer is set with the required pass/fail criterion for acceptance of the test assembly.
Please contact us at Davis Scientific Treatments, if you need any advice on a specific leak testing application.