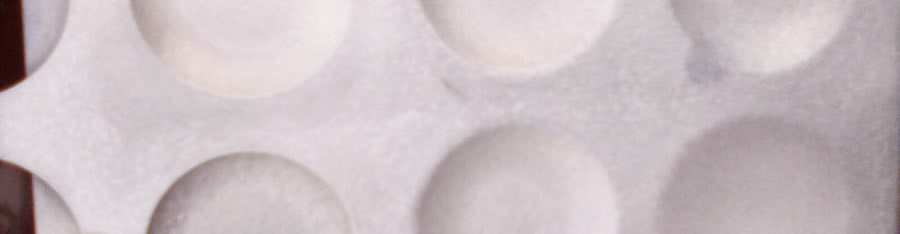
Aluminium Brazing - Recent Developments
Use of Cladding Alloy Foils
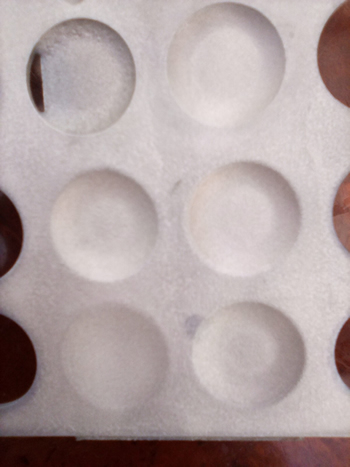
- Photograph shows 2 aluminium plates vacuum brazed using 4045 foil faced aluminium alloy
- Note the full continuous brazed fillet in each hole
- This process can be used for fabrication of parts to make assemblies, where welding cannot be used, nor components dip brazed
Davis Scientific Treatments Ltd has been offering aluminium brazing of components, processed under vacuum conditions, since 2013. In that time DST has acquired considerable knowledge in the field, through experimentation and innovation.
For many low to medium volume applications, we can provide production facilities, after R & D developments have been completed successfully.
Being a fairly small company, sometimes there are large production requirements involved, for which we can still carry out preliminary R & D work, to prove the necessary techniques for production.
In these cases, DST is always very pleased, after trials phase, to act as consultants, guiding companies towards the implementation of full production.
The following notes give an insight into the recent developments of aluminium brazing at DST.
Introduction
For many years, we have been brazing successfully aluminium components and sub-assemblies. In this time, we have developed techniques for using various types of interleaving foils, in order to improve joint quality.
Occasionally we have used pastes, where conditions dictate, to obtain acceptable results.
The use of foils has given many satisfactory joints with aluminium parts. The foil melts and flows, during the brazing process, to provide on cooling a metallic bond between the components.
Use of Cladding Foils
In recent years, aluminium core material has become available, with a thin cladding of an aluminium alloy, suitable for brazing.
There are choices of alloy composition of both the base material and the cladding. This latter is conventionally available with the thickness in the range 5 to 15 % of core material thickness. It can be obtained in coil and sheet form, with cladding on only one side, or on both.
As mentioned above, the cladding alloy acts on brazing to form a metallic bond between the components.
Another clear advantage, especially in volume production, is in the formation of the joint profile, which of course must exactly match the shapes of the components. This shape can be automatically created, during the process of manufacture of the base material component itself. Otherwise, making the foil interleave from sheet, for example, is a time consuming, and therefore expensive, operation.
Aluminium/Silicon Cladding Alloys
On the phase diagram of Al/Si alloys, a Silicon content of 12.6 % gives the lowest, eutectic, liquidus temperature, of about 577 deg C.
4045 has about 10-11 % Silicon, and with AA4047, about 12-13 %. Correspondingly, use of 4045, a popular cladding alloy, requires a slightly higher brazing temperature, with a higher melting range.
Although 4045 has a lower fluidity, we at DST have been able to obtain very satisfactory joints, at temperatures well below the general aluminium melting point.
Aluminium Heat Exchangers
A rapidly growing market for Aluminium brazing is in construction of heat exchanger units. Not only are they needed for aerospace and industrial applications, but the increased use of electric vehicles require cooling of lithium based batteries.
The use of aluminium is preferred:
- high strength
- corrosion resistance
- formability
- low weight
Often the components are made from, typically, AA3000 or AA6000 series Aluminium, clad with 4004, 4343, or 4045 Al/Si alloy. The core material provides structural integrity for the assembly.
Silicon Diffusion
At brazing temperatures, Silicon from the cladding alloy can diffuse into the base material. Core material penetration reduces strength and corrosion resistance. Loss of silicon from cladding has adverse affect on brazing flow properties.
The amount of this penetration depends on:
- temperature
- brazing time
- silicon content of core material
- silicon content of cladding alloy
AA3003 has lower Silicon content, so diffusion is reduced. It is more pronounced in 6000 series alloys.
Cladding sheet with Barrier Layer
For heat exchangers, high strength multilayer sheets are now available. Sandwiched between the cladding alloy, and base material, a thin layer of, typically, pure aluminium in interleaved.
This barrier provides a physical separation between cladding and core. It acts to prevent the interaction between liquid and solid, within the melting range. The solid diffusion of Silicon is reduced, between the cladding and the base material.